It's been a while. I've been lurking and soaking up info but haven't posted in a bit. I've had several projects to get behind me and now I have a good one on the boat - time for a new floor. I'll post a full report when it's done but right now I need a little advice. I pulled the old plywood floor out - rotten piece of...
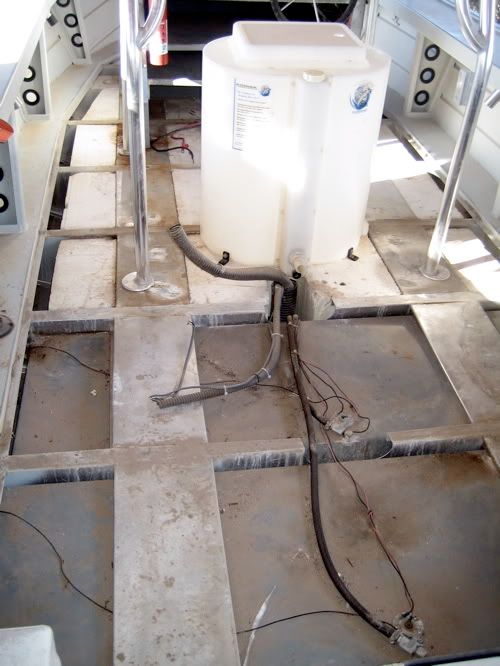
Anyway, as you can see in the first photo there are some 12" wide floor plates welded between the bulk heads. I'm not sure how much structural help they give but there they are. The center console and T-top were lag bolted to the plywood and through these plates. It seems the flexing of the T-top poped the welds on the floor plate it was lagged to.
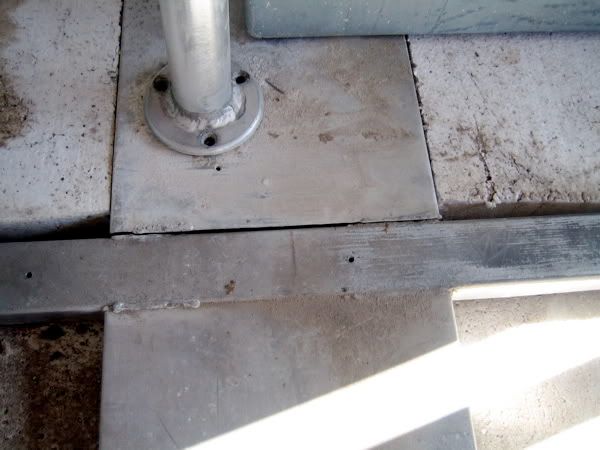
Here is where I need some advice. How would you fix it? Simply re-weld? Add some aluminum angle iron below and weld? or epoxy? Is there any cause for concern throwing a welder on the older aluminum or any advice on how to weld it?
When I got the boat the T-top only had four legs - I added the back two eliminating the flex the T-top used to have so it shouldn't exhibit the same force in this area again.
Next question; how would you attatch the T-top and the console to the new floor? Lag again? T-nuts?
Many thanks in advance for any advice!