Welders
- Gypseas
- Donator 14, 15
- Posts: 154
- Joined: Sat Oct 22, 2011 12:23 am
- 12
- Your location: Victoria, BC
- Contact:
Welders
Ready to purchase a welder that would be capable of doing aluminum.
What do you guys use out there?
MIG w push/pull gun, TIG ? Am thinking small projects, say up to 1/4 inch, would be nice to do stainless as well.
Thank you for your input.
What do you guys use out there?
MIG w push/pull gun, TIG ? Am thinking small projects, say up to 1/4 inch, would be nice to do stainless as well.
Thank you for your input.
- goatram
- Donator 08, 09, 10, 11, 12, 13, 14, 15, 16, 17, 18, 19
- Posts: 1959
- Joined: Wed Apr 09, 2008 11:53 pm
- 16
- Your location: Stanwood, Wa
- Location: Stanwood WA
Re: Welders
I have this one for my TIG
http://www.millerwelds.com/products/tig/syncrowave_200/
For my MIG I use the older Miller 250 that I got at a auction. My spool gun bought new from Central Welding.
http://www.millerwelds.com/products/mig ... del=M00218
The machine to weld the laid down dimes is this one. I want one. $6000 set up to weld Alloy to half inch. Production weld a boat type of machine
http://www.millerwelds.com/products/mig ... del=M00151
Lincoln has similar machines
http://www.millerwelds.com/products/tig/syncrowave_200/
For my MIG I use the older Miller 250 that I got at a auction. My spool gun bought new from Central Welding.
http://www.millerwelds.com/products/mig ... del=M00218
The machine to weld the laid down dimes is this one. I want one. $6000 set up to weld Alloy to half inch. Production weld a boat type of machine
http://www.millerwelds.com/products/mig ... del=M00151
Lincoln has similar machines
John Risser aka goatram
33' RBW with twin 250 Hondas (Aliens)
2015 Ford F350 Dually
Master of R&D aka Ripoff and Duplicate
33' RBW with twin 250 Hondas (Aliens)
2015 Ford F350 Dually
Master of R&D aka Ripoff and Duplicate
Re: Welders
My tig is a syncrowave 250 and my gun is a pulse, 350P both work awesome for boat builds
-
- Posts: 67
- Joined: Tue Jan 10, 2012 4:20 pm
- 12
- Your location: New Zealand
- Location: New Zealand
- Contact:
Re: Welders
Used a 350P. Decididly average and I'd consider it a higher end domestic welder.
Have been using Fronius welders since '99. Put at least 350lbs of welding wire (1.2mm or 0.047") before tip changes. Usually replace tip due to wear rather than burn-backs, which are rare. Has programs to weld alot of metals, amoung them AlMg5, AlSi, Al99%, hardfacing, CrNi, copper, titanium... They are a digital machine so have excellent repeatability. "Hot-start" option for up to 150% of heat for a programmable amount of time during arc start-up. "Soft-Start" for Spatter Free Ignition (SFI).
It is a transpulse synergic machine rated to 270amps. Does up to about 9/16" plate. Power pack and wire feed in one compact box. We just use the air-cooled PPU5 torch. Comes with up to 33' (10m) of lead (which I use) meaning I can get anywhere on the boat without having to relocate the welder.
Welder
http://www.fronius.com/cps/rde/xchg/SID ... G_HTML.htm
Torch
http://www.fronius.com/cps/rde/xchg/SID ... G_HTML.htm

Bottom weld is .190 to .190. Top one is .190 to .100
Have been using Fronius welders since '99. Put at least 350lbs of welding wire (1.2mm or 0.047") before tip changes. Usually replace tip due to wear rather than burn-backs, which are rare. Has programs to weld alot of metals, amoung them AlMg5, AlSi, Al99%, hardfacing, CrNi, copper, titanium... They are a digital machine so have excellent repeatability. "Hot-start" option for up to 150% of heat for a programmable amount of time during arc start-up. "Soft-Start" for Spatter Free Ignition (SFI).
It is a transpulse synergic machine rated to 270amps. Does up to about 9/16" plate. Power pack and wire feed in one compact box. We just use the air-cooled PPU5 torch. Comes with up to 33' (10m) of lead (which I use) meaning I can get anywhere on the boat without having to relocate the welder.
Welder
http://www.fronius.com/cps/rde/xchg/SID ... G_HTML.htm
Torch
http://www.fronius.com/cps/rde/xchg/SID ... G_HTML.htm

Bottom weld is .190 to .190. Top one is .190 to .100
-
- Donator 08, 09, 10, 11, 12, 13, 14, 15, 16, 17, 18, 19, 20, 21, 22, 23, 24
- Posts: 1762
- Joined: Mon Aug 18, 2008 1:37 am
- 15
- Your location: Kenai, AK
- Location: Kenai, Alaska
Re: Welders
Gypseas,
first MIG: if you'll be doing lots of welding ( more than one boat ) then a push pull MIG wire feed will turn out to be the better wire feed system. But, if you'll be doing tanks/brackets/and repairs and maybe one boat every so often? Then, the pistol or T shaped "1lb." gun is the wiser investment. My reasoning is the smaller push only 1lb. gun will do lots of work for a price of less (many times) 1/10th the cost of the push-pull system.
MK Products ( http://mkproducts.com/ )makes a good pistol style or 1lb. gun and they make fine push pull systems, but there are plenty of other reliable wire feeders on the market.
MIG power supplies are designed to keep Constant Voltage (CV) constant so the uniformly fed wire will 'burn' (convert to molten droplets in the arc) evenly and therefore allow an even weld bead. Some power supplies will provide CV ... AND.. Constant Current that is used for TIG. But... those power supplies most offer only supply CC in DC not AC used to TIG weld aluminum.
I'm not aware of any major welding power supply manufacturer in the US that offers CV/CC with AC CC output, so that is why most shops have one DC MIG power supply CV and one CC TIG inverter for AC TIG work in non-ferrous alloys.
A better description of exactly what you'll be building would make a reply more informed?
next AC TIG.
Anytime you work in smaller welds- not 20' long hull seams- you can very effectively use AC TIG to an advantage over MIG. Even with the newer 'smart' and programmable MIG power supplies which produce very specific beads for different metal alloys, thicknesses and wire sizes; TIG can provide a slowed down control of the weld not possible with MIG.
MIG's wire must be feeding to give the arc and it therefore has to deliver filler (molten wire) to maintain an arc. So you must move the welder to have any heat of fusion as there is wire piling up on the weld area. But with AC TIG you can stop adding filler, and just keep the puddle molten and this allows you to fuse areas that are different thicknesses along the weld, it allows you to tie in easier in complex corner joints and it allows you to move at the pace you set instead of the related rated set by the MIG wire feed and arc.
Another aspect common to TIG is the constant adjustment done by the welder at the torch. This remote current control means that you'd naturally get in the habit of making minute current adjustments to the welds and therefore 'tune' the amperage to each puddle; in MIG we usually set the output both wire speed and voltage and 'just weld'.
My personal preferences are Miller TIG power supplies and Lincoln MIG welders, as I like the controls and arc characteristics of each brand's products in those categories best. I do understand there are several lower cost (compared to Miller/Lincoln) power supplies on the market, but I have not welded with them and can't speak about their performance. My use makes longest term reliability worth a higher cost so I don't even shop these other brands, but they are widely used and will perform good service and should be considered if you're just starting out?
I think the Miller Dynasty series TIG power supplies are the best US made TIG power supplies and I prefer the Power MIG 350 from Lincoln for the controls it delivers in MIG. I have used MK push pull guns since the 1970's and have current models of these products now.
Now, to add some conditions to these remarks. Both Miller and Lincoln have included arc control features in the power supplies mentioned that require some extensive (100's if not 1000's of hours) practice/experience/knowledge to use effectively.
If you buy a digital camera with 100 features and menus that go on for 20 pages, will you have the photographic experience to use them? I would not, I buy and use the simplest point and shoot compact models because I am not going to spend time learning to make use of the more advanced functions.
I you buy a new digital sound system with a mixing board and more effects and controls than a Space Shuttle pilot console- do you have that audio knowledge to use all that? Are you interested in getting the high end system to learn? I'm not, I use the PC to play back a few tunes and listen to Emmylou or Patsy on the little MP3 player under my earphones in the shop.
Most of the guys I know with the higher end and that means feature laden power supplies won't take the many hours needed to learn to use all the features so they've wasted money in my view. If you'll take time to experiment, test and learn to use the features I've said are worth my time (above) then the advice I give may be worth considering.
so to continue this analogy, are the high end features of a complex welding arc control power supply worth the costs if you don't have the experience and practice time to effectively use them?
If you're more likely to just 'get welding' then I'd look for used equipment that was reliable and less complex. In the first few hundred hours of welding most people will do better to stay with fundamentals and basic welds instead of being frustrated by lots of bells and whistles that their reflexes are not yet trained to use.
On the other hand, if you do have the more advanced features they can help shorten learning time drastically. The Catch22 involved in using the features is that you'd have to have lots of experience to clearly understand how and why they work. A way around this seeming contradiction is instruction. But then most of the community college level courses I've seen target such basics they instructors don't provide higher end or detailed welding knowledge needed to see the advanced arc (puddle) controls' benefits and applications.
I think this decision, about which power supplies to acquire, is best coupled to the work you plan to do.
Cheers,
Kevin Morin
first MIG: if you'll be doing lots of welding ( more than one boat ) then a push pull MIG wire feed will turn out to be the better wire feed system. But, if you'll be doing tanks/brackets/and repairs and maybe one boat every so often? Then, the pistol or T shaped "1lb." gun is the wiser investment. My reasoning is the smaller push only 1lb. gun will do lots of work for a price of less (many times) 1/10th the cost of the push-pull system.
MK Products ( http://mkproducts.com/ )makes a good pistol style or 1lb. gun and they make fine push pull systems, but there are plenty of other reliable wire feeders on the market.
MIG power supplies are designed to keep Constant Voltage (CV) constant so the uniformly fed wire will 'burn' (convert to molten droplets in the arc) evenly and therefore allow an even weld bead. Some power supplies will provide CV ... AND.. Constant Current that is used for TIG. But... those power supplies most offer only supply CC in DC not AC used to TIG weld aluminum.
I'm not aware of any major welding power supply manufacturer in the US that offers CV/CC with AC CC output, so that is why most shops have one DC MIG power supply CV and one CC TIG inverter for AC TIG work in non-ferrous alloys.
A better description of exactly what you'll be building would make a reply more informed?
next AC TIG.
Anytime you work in smaller welds- not 20' long hull seams- you can very effectively use AC TIG to an advantage over MIG. Even with the newer 'smart' and programmable MIG power supplies which produce very specific beads for different metal alloys, thicknesses and wire sizes; TIG can provide a slowed down control of the weld not possible with MIG.
MIG's wire must be feeding to give the arc and it therefore has to deliver filler (molten wire) to maintain an arc. So you must move the welder to have any heat of fusion as there is wire piling up on the weld area. But with AC TIG you can stop adding filler, and just keep the puddle molten and this allows you to fuse areas that are different thicknesses along the weld, it allows you to tie in easier in complex corner joints and it allows you to move at the pace you set instead of the related rated set by the MIG wire feed and arc.
Another aspect common to TIG is the constant adjustment done by the welder at the torch. This remote current control means that you'd naturally get in the habit of making minute current adjustments to the welds and therefore 'tune' the amperage to each puddle; in MIG we usually set the output both wire speed and voltage and 'just weld'.
My personal preferences are Miller TIG power supplies and Lincoln MIG welders, as I like the controls and arc characteristics of each brand's products in those categories best. I do understand there are several lower cost (compared to Miller/Lincoln) power supplies on the market, but I have not welded with them and can't speak about their performance. My use makes longest term reliability worth a higher cost so I don't even shop these other brands, but they are widely used and will perform good service and should be considered if you're just starting out?
I think the Miller Dynasty series TIG power supplies are the best US made TIG power supplies and I prefer the Power MIG 350 from Lincoln for the controls it delivers in MIG. I have used MK push pull guns since the 1970's and have current models of these products now.
Now, to add some conditions to these remarks. Both Miller and Lincoln have included arc control features in the power supplies mentioned that require some extensive (100's if not 1000's of hours) practice/experience/knowledge to use effectively.
If you buy a digital camera with 100 features and menus that go on for 20 pages, will you have the photographic experience to use them? I would not, I buy and use the simplest point and shoot compact models because I am not going to spend time learning to make use of the more advanced functions.
I you buy a new digital sound system with a mixing board and more effects and controls than a Space Shuttle pilot console- do you have that audio knowledge to use all that? Are you interested in getting the high end system to learn? I'm not, I use the PC to play back a few tunes and listen to Emmylou or Patsy on the little MP3 player under my earphones in the shop.
Most of the guys I know with the higher end and that means feature laden power supplies won't take the many hours needed to learn to use all the features so they've wasted money in my view. If you'll take time to experiment, test and learn to use the features I've said are worth my time (above) then the advice I give may be worth considering.
so to continue this analogy, are the high end features of a complex welding arc control power supply worth the costs if you don't have the experience and practice time to effectively use them?
If you're more likely to just 'get welding' then I'd look for used equipment that was reliable and less complex. In the first few hundred hours of welding most people will do better to stay with fundamentals and basic welds instead of being frustrated by lots of bells and whistles that their reflexes are not yet trained to use.
On the other hand, if you do have the more advanced features they can help shorten learning time drastically. The Catch22 involved in using the features is that you'd have to have lots of experience to clearly understand how and why they work. A way around this seeming contradiction is instruction. But then most of the community college level courses I've seen target such basics they instructors don't provide higher end or detailed welding knowledge needed to see the advanced arc (puddle) controls' benefits and applications.
I think this decision, about which power supplies to acquire, is best coupled to the work you plan to do.
Cheers,
Kevin Morin
kmorin
-
- Doator '08, '09, '10, '11, '12, '13, '14, '15, '16, '17
- Posts: 177
- Joined: Tue Mar 24, 2009 7:12 pm
- 15
- Your location: Gulfport, Fl
Re: Welders
Has anyone seen one of these in action in real life, not just youtube?
http://www.multiplaz.com/about
http://www.multiplaz.com/about
"It was the Law of the Sea, they said. Civilization ends at the waterline.
Beyond that, we all enter the food chain, and not always right at the top."
Hunter S. Thompson
Beyond that, we all enter the food chain, and not always right at the top."
Hunter S. Thompson
- Gypseas
- Donator 14, 15
- Posts: 154
- Joined: Sat Oct 22, 2011 12:23 am
- 12
- Your location: Victoria, BC
- Contact:
Re: Welders
Thank you all for your input.
KMorin as always a very informative and thoroughly thought post, thank you for taking the time.
Mostly interested in doing small projects, small repairs on the boat, looks like a TIG would be the way to go .
Let ya know
cheers
KMorin as always a very informative and thoroughly thought post, thank you for taking the time.
Mostly interested in doing small projects, small repairs on the boat, looks like a TIG would be the way to go .
Let ya know
cheers
-
- Donator 08, 09, 10, 11, 12, 13, 14, 15, 16, 17, 18, 19, 20, 21, 22, 23, 24
- Posts: 1762
- Joined: Mon Aug 18, 2008 1:37 am
- 15
- Your location: Kenai, AK
- Location: Kenai, Alaska
Re: Welders
Gypseas, if your longer welds are anticipated to be 6"- maybe a foot? Then TIG will be more versatile overall.
I don't say it will be as easy to learn to use as MIG- but it will be the more utilitarian weld in aluminum for small work.
Do you have hood time in any arc welding? or gas welding? This helps to plan your self training time and practice sessions.
Cheers,
Kevin Morin
Kenai, AK
I don't say it will be as easy to learn to use as MIG- but it will be the more utilitarian weld in aluminum for small work.
Do you have hood time in any arc welding? or gas welding? This helps to plan your self training time and practice sessions.
Cheers,
Kevin Morin
Kenai, AK
kmorin
- Gypseas
- Donator 14, 15
- Posts: 154
- Joined: Sat Oct 22, 2011 12:23 am
- 12
- Your location: Victoria, BC
- Contact:
Re: Welders
Friend of mine has the Lincoln 225 and let me try it.
I do my share of brazing at work (refrigeration) and so far TIG seems pretty easy, just like brazing with an electric flame so to speak. The roll of dimes I haven't gotten yet, but working on it.
As for projects in the near future: fish-hold around 4ft long weld, anchor caddy, some handrails, downrigger extensions, re-do the rod holders, nothing too big just yet.
Thank you for guidance.
I do my share of brazing at work (refrigeration) and so far TIG seems pretty easy, just like brazing with an electric flame so to speak. The roll of dimes I haven't gotten yet, but working on it.
As for projects in the near future: fish-hold around 4ft long weld, anchor caddy, some handrails, downrigger extensions, re-do the rod holders, nothing too big just yet.
Thank you for guidance.
- Gypseas
- Donator 14, 15
- Posts: 154
- Joined: Sat Oct 22, 2011 12:23 am
- 12
- Your location: Victoria, BC
- Contact:
Re: Welders
Guess a year's past already, took me that long to actually push the button
So Friday they made me a deal I could not say NO to. Ended up buying this:
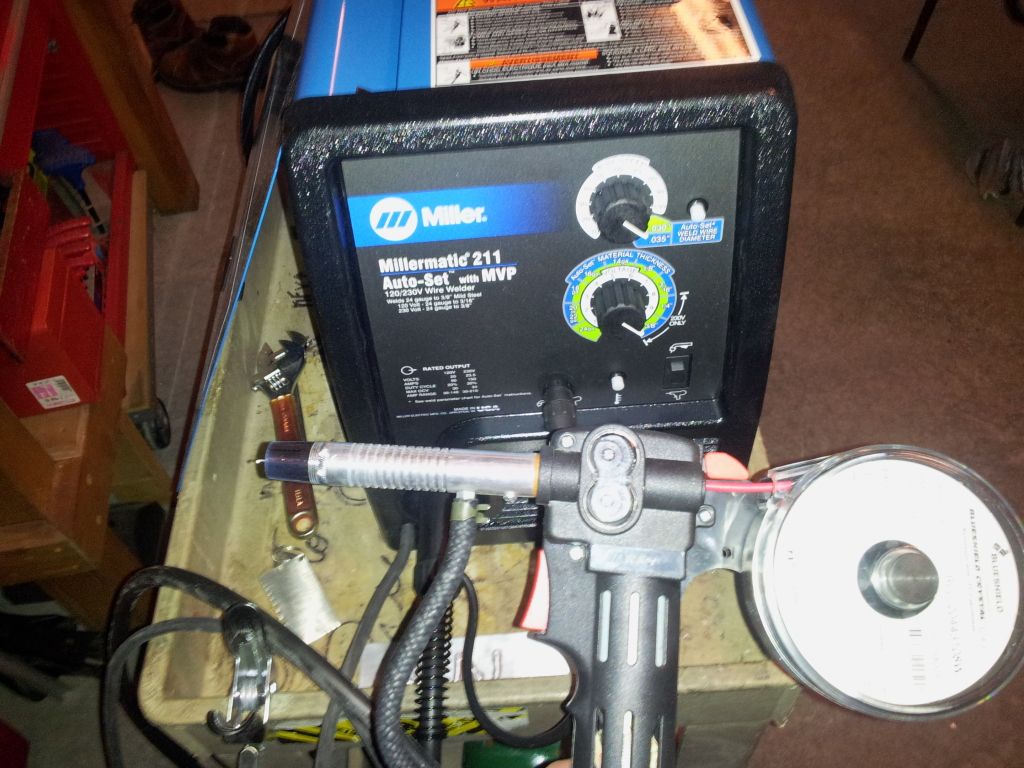
Been playing with it yesterday most of the day and some today and can say that it is not as easy as the vids on youtube.
Tried to weld 3/16 angle to 3/16 plate using the guide on the inside cover to no avail. Played the wire speed, voltage and argon pressure on the reg up/down burned a half a dozen or so tips.
Any tips that you guys may want to share to help me save my sanity

1/4 on 1/4 by 2inch

This is yesterdays using 120V, compared to 230V used today in above pics.




So Friday they made me a deal I could not say NO to. Ended up buying this:
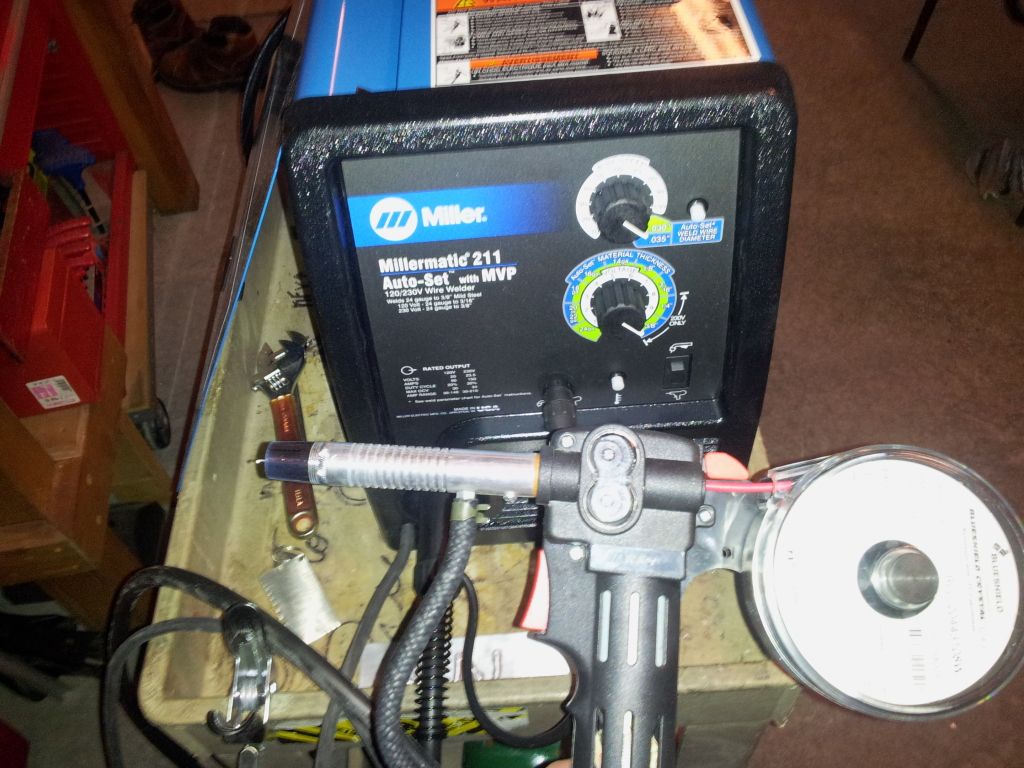
Been playing with it yesterday most of the day and some today and can say that it is not as easy as the vids on youtube.
Tried to weld 3/16 angle to 3/16 plate using the guide on the inside cover to no avail. Played the wire speed, voltage and argon pressure on the reg up/down burned a half a dozen or so tips.
Any tips that you guys may want to share to help me save my sanity


1/4 on 1/4 by 2inch

This is yesterdays using 120V, compared to 230V used today in above pics.
